Tim Garner, MiTek UK & Ireland Commercial Director, discusses the role of offsite construction in supporting the delivery of UK housing targets.
Can MMC help housebuilders deliver more homes, more efficiently?
The government’s ambition to see at least 300,000 new homes built every year by the mid-2020s was always going to be challenging, even without the impact of Covid-19.
And with latest estimates suggesting the annual target may now be as high as 345,000, the wider industry is having to think differently about how these goals can be met.
It seems clear that if this moving target is going to be realised, the industry needs to call on all the tools it has available: and that means exploring all the benefits that modern methods of construction (MMC) have to offer.
We’re not suggesting anything particularly radical or new. Back in September 2020, the ‘Build Homes, Build Jobs, Build Innovation’ report set out a blueprint for a housing-led industrial strategy with MMC at its heart.
It calls on the government to make a modular, MMC and off-site approach the driving force behind Boris Johnson’s ‘build, build, build’ agenda, saying that with the right support, the industry has capacity to build 75,000 new modular homes a year by 2030 – at the same time creating 50,000 new jobs, reducing carbon emissions by 40% and helping to level up regional economies.
What a fantastic opportunity, and to us it makes perfect sense. At MiTek we’re seeing a growing global market for MMC, particularly in the housebuilding sector, as companies recognise the range of benefits offered by MMC, from improved environmental credentials to reduced costs and construction timescales.
The good news is that there are already major players in the UK MMC market providing sought-after tried and tested, high quality products. And it’s clear that there is now greater confidence and positivity about the role of MMC and off-site.
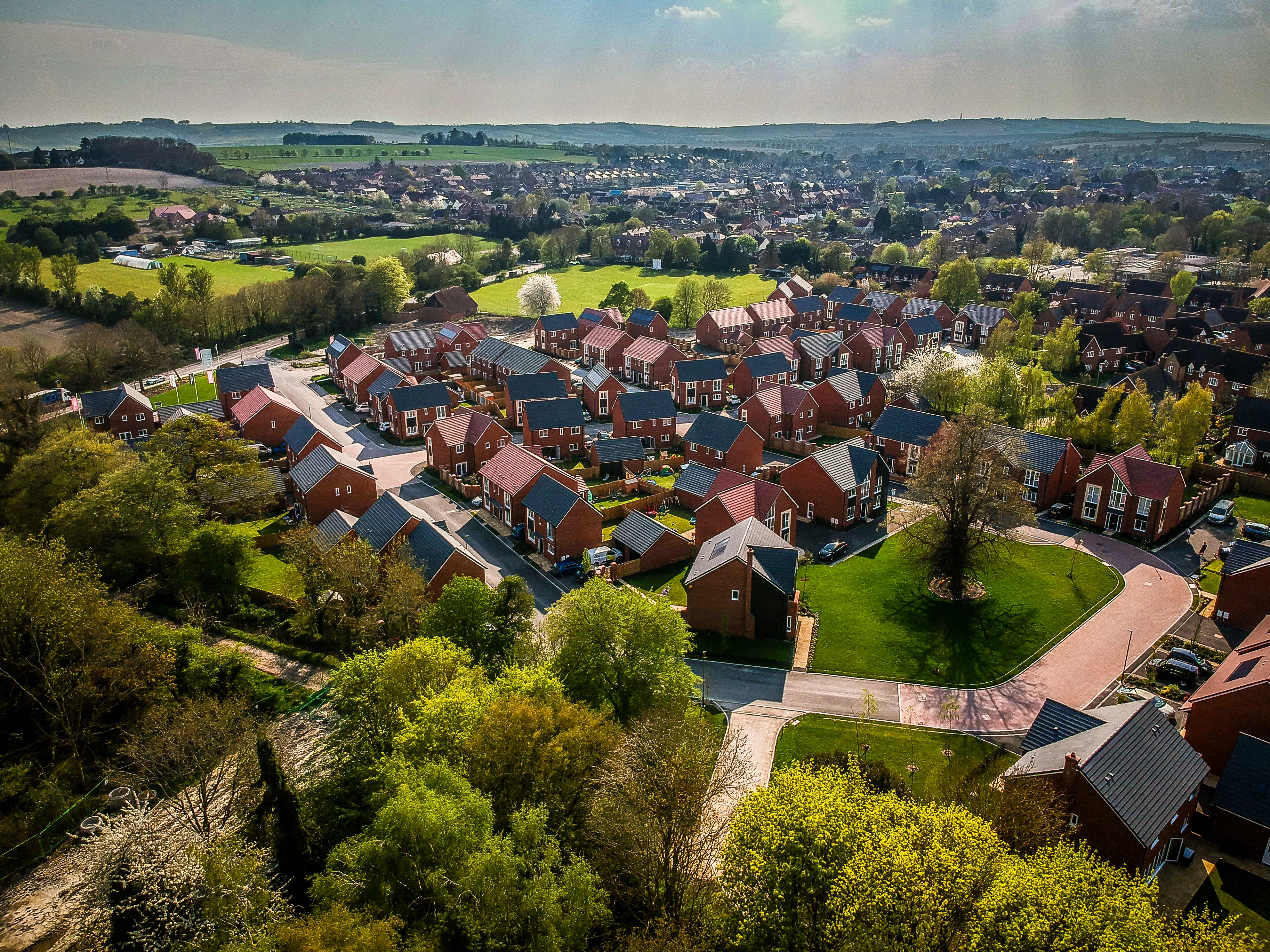
Housebuilders are seeking out more MMC components
Our Posi-Joist product is a great example, having already been used in well over 250,000 projects here in the UK and Ireland, since it was first introduced in 1999. Once awareness of a product increases, and it becomes a trusted and accepted solution, so do the numbers.
The growth of Posi-Joist over the last decade, and the last five years in particular has been truly impressive, increasing from around 10,000 units in 2010 to around 30,000 units in 2020, on both traditional and MMC builds.
Posi-Joists are widely specified across a variety of construction methods and work particularly well with MMC and modular construction techniques. Custom end details and the freedom provided by the open web service void allow for great flexibility, and the increasing use of ‘Posi-Joist cassettes’ allows for even greater offsite construction and time savings on site.
Building homes using MMC is quicker, safer, more reliable and more environmentally-friendly than traditional housing construction methods. As much of the component construction required for a modular build takes place off site, the process is more efficient, is quicker, reduces waste and makes the ‘just in time’ supply chain far more manageable. The process is also set up in a way that means it has been able to continue even during the constraints caused by the pandemic.
The basic production model for new homes is changing
According to the NHBC, there is a common desire to improve predictability in terms of cost, time and quality – something that MMC is known for delivering. As businesses increasingly recognise that the basic production model for new homes needs to change, so the appetite for MMC is growing.
This increased interest is reflected in a rise in the average ‘premanufactured value’ (PMV) of schemes. The gradual reduction in the proportion of site labour required and associated site overheads is being driven by a combination of different techniques – from volumetric modular solutions through to more subtle changes in component or sub-assembly level standardisation.
All these routes have equal validity and are part of our industry’s journey towards integrating a blend of both offsite and onsite manufacturing with traditional site-based construction, achieving the best of both worlds.
We believe boosting the modular and MMC housing sector will help solve a number of the UK’s long-term challenges, from addressing the slow pace of housing supply and low productivity, through to helping reduce the sector’s contribution to the UK’s carbon footprint.
Solutions like made-to-measure Posi-Joists which combine the versatility of timber with the strength of steel webs to produce strong, clear spanning and lightweight floor and roof systems have a vital role to play in a new MMC world.
It’s innovation and applications like these that will ensure quality, robust homes can be built in a cost-effective, efficient and environmentally responsible way … and help bring that 345,000 new homes a year target within reach.
Find out more about Posi-Joist; or use our interactive span checker to identify the Posi-Joist suitable for your project. Find your nearest manufacturer, or email us at: [email protected]