Posi-Joist is helping professionals from every trade do their jobs to the best of their ability, saving precious time in labour costs. See the positive impact it’s having on one Surrey development.
2025 is coming a lot faster than many realise. With it will come mandatory Future Homes Standard (FHS) compliance for new builds. These regulations will ensure the houses of tomorrow produce 75-80% less carbon.
From heating to hot water systems to insulation, today’s building technologies are being critically re-examined. Alongside other legislation targeting existing homes, these measures should help the UK achieve its 2050 net zero target.
But some housebuilders aren’t waiting until then, in fact they’re not even waiting for 2025. Builders like Croudace Homes are trialling new technologies and cutting carbon right now, using industry-leading solutions like Posi-Joist, says Site Manager, Matthew McCourt:
“With the Future Homes Standard, the market for Posi-Joist is going to grow.”
“It’s going to be very difficult to achieve the new regulations using similar products such as I Beams or I Joist.” He says additional room is going to be needed for services to pass through the ceiling void:
“We’re going to have a lot more additional services passing through the joists, such as pipework, cabling and additional ducting. At the moment Posi-Joists are the only product on the market that can facilitate that.”

Setting the standard in homebuilding
Founded in 1946, Croudace are five-star residential developers with a strong presence across the South East. They’re well ahead of the booming nationwide demand for Posi-Joist, having specified it exclusively in their homes for over 14 years. We visited their Firethorn Place project in Ewhurst, Surrey, to find out why.
The housing development has all the Croudace hallmarks – a strong design aesthetic inside and out, maximum green space and high-quality build and specification of materials. Every last detail is considered, and it shows.
At Firethorn Place, joists arrive on site ready to be installed. Made offsite by timber engineering specialist Crendon, there is no need even to drill anything. It’s a safer, far more efficient way of working. Croudace homes get a level of consistency and quality which sets them apart. “One of our main priorities is quality” says McCourt:
“Posi-Joist has good dimensional stability so they’re a lot less susceptible to twisting and warping. They have good span capabilities which allows us to plan the layout of our homes better so we can have more open plan living like the home we’re sitting in now.”
Croudace believes Posi-Joists are much more versatile than other products out there on the market.
“They’re much more adaptable than i-joists. When it comes to the first fix stage inside the property, Posi-Joists are much easier to work with. The electrician and the plumber find it much easier to run their cabling and pipe work through. And we know it saves time.”
And of course, collaboration sits at the heart of what Croudace do. Different professionals from a range of trades need to do their jobs as quickly and efficiently as possible. Posi-Joist is streamlining the process, going so far as to provide clear zones for each trade’s input. There’s no potential for services to clash over space.
Trades are saving about a day or two of installation time each. That translates to incredible time and labour cost savings across a whole development. We got to speak to representatives from three of these trades to hear more about working with Posi-Joist.
Mike Armstrong and Chris Doldins, SCC Carpentry
Mike has been using Posi-Joist for 15 years, and Chris for 12. It’s a lighter, more manageable solution compared to traditional joists. Components arrive prefabricated, ready to be placed.
To Mike, that’s huge: “Posi-Joist saves around two days of labour per installation. Obviously, that’s quite significant compared to old-style joists, but Posi is also straighter; there’s less movement. They’re easier to store safely, too. It’s a better-engineered solution all round.
“In fact, it’s the best joisting system on the market right now; I’d put it in my own house if I had the option. The Posi market can only grow and grow from here. Other trades who follow on from us, plumbers and electricians, maybe see even more benefits than we do.”
Chris, meanwhile, was quick to emphasise Posi-Joist’s positive impact on workflow. “The components always come in the same dimensions as the building you’re working on. So, you know you’re not spending time cutting joists to size and kicking up a lot of sawdust.
“Each joist arrives already marked for installation. You can plan exactly when you’ll need to put each component in, it’s possible to keep workspaces less cluttered. That’s good for overall safety. And really, Posi-Joist is just nice to work with. They’re light, you can grip them more easily by the metal webbing.
“When you add up all these benefits, the time you’re saving gets impressive. I can’t see a scenario where housebuilders would reasonably go back from using it.”
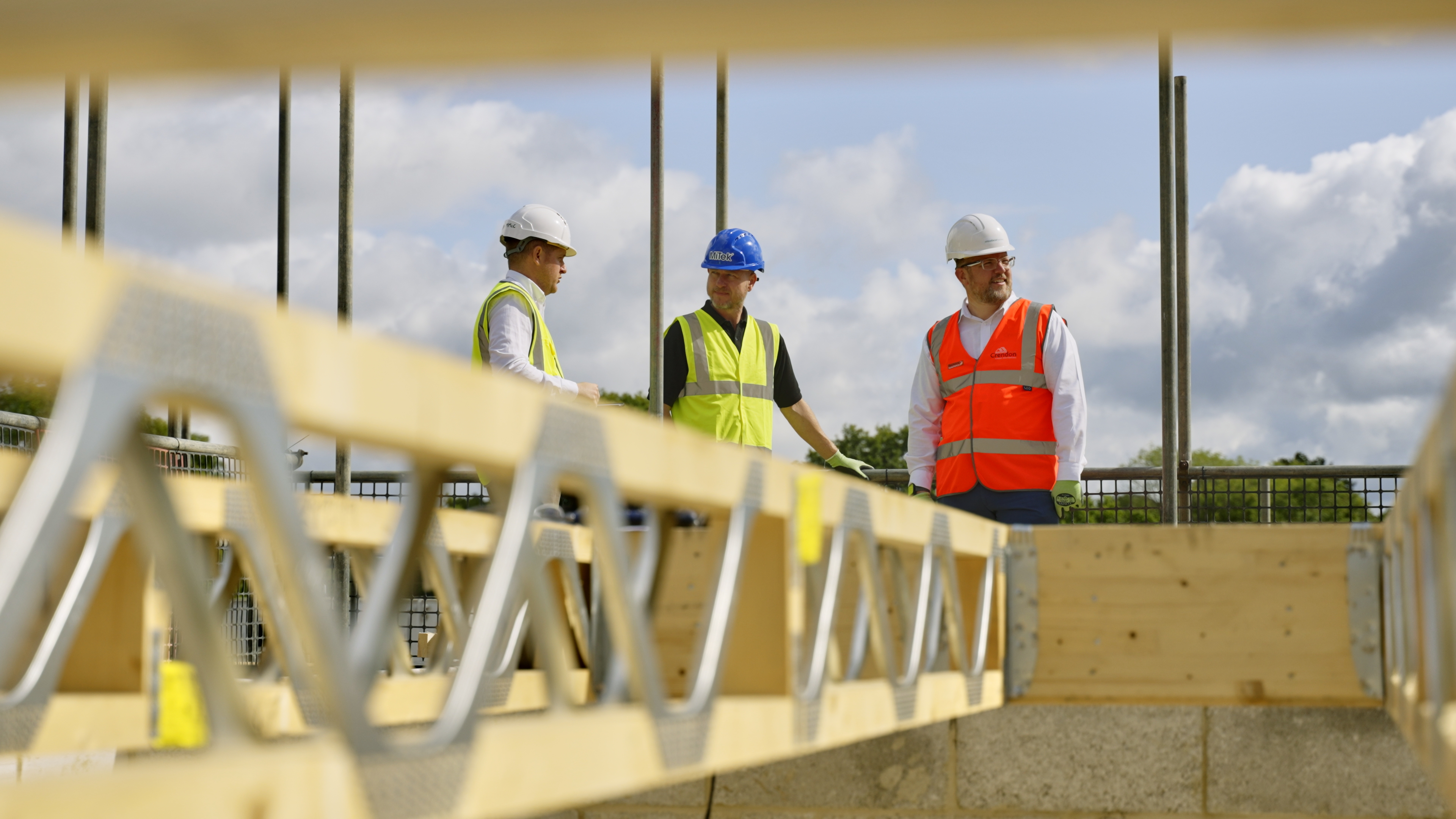
Sam Edwards, Goring Electricals
Despite already using Posi-Joist for 10 years himself, Goring’s Sam still has one eye on its role in the future. For him, the FHS means planning to incorporate more technologies like MVHR. He talked us through what that would typically mean.
“With an old I-Beam or regular joist, there’s a lot more labour involved. You’ve got to drill out space for things, so you’re producing waste on site. Where does it go? There’s a potential safety concern. Meanwhile, everyone else is doing the same thing so you might end up competing for space.
Compare that to a nice Posi-Joist. There’s plenty of room for everyone to work with it. We can run our cables straight through, or tie them if they’re parallel to the joist. When the guys come in and see we’re using it, they’re generally a bit happier.
So there’s three big benefits; it’s easier, you save time, and you can work together more easily with people doing other jobs.”
Dan Sanders, PRS Plumbing
With considerable expertise on the tools, Dan is used to working efficiently. But Posi-Joist is also saving him hours per day on top of his own methods. That’s vital when he’s working with complex FHS-compliant designs that use a lot of high-tech components.
In his own words, “I can get long lengths of pipe through less fitting using Posi-Joist. It works more flexibly; in the real world, you’re never going to be able to match the design 100% all the time. Posi lets us adapt, with less drilling, and still keep pipework together neatly. We don’t step on anyone’s toes when we’re using it.
I’ve heard people look at the upfront costs and get cold feet. I’d advise them to think about what they’re saving in labour costs, time, wastage, and so on. It’s not only a compliance thing, we’re talking about a sound investment that makes life easier for everyone on site. That’s been my experience.”
Collaborate, conceive, construct: Rethinking UK property
Only industrywide teamwork can help professionals like these navigate upcoming challenges and new legislation. MiTek is working closely with industry to drive sustainable, efficient design.
Looking at proposed house plans, the team suggests improvements to optimise design, whether that’s introducing Posi-Joist, or elevating designs which already specify the right components. Most importantly, we can communicate the benefits to the right stakeholders and secure savings in time, material, and cost.
Partnerships like this are helping get the best components in the hands of the best-qualified people. The result will be better, more sustainable housing, and we’re proud to play our role in building that future.